China should emulate the quality management Japan has brought to manufacturing industries in the United States.
Mitsuru Kawai,
As of January 1, 2018
- Supervisor of plants across in-house companies
- Chief Officer , Safety & Health Promotion Division
Mitsuru Kawai was born January 2, 1948. He graduated from Toyota Technical Skills Academy in March 1966 and joined Toyota Motor Corporation (TMC) in March the same year.
Mr. Kawai was appointed project general manager of the Forging Division of the Honsha Plant in January 2005, and in June the same year he became general manager of the division. In January 2008, he was made a deputy plant manager of the Honsha Plant. In January 2013, Mr. Kawai was made a senior technical executive. In April 2015, he became senior managing officer and, executive vice president of the Unit Center and deputy chief officer of the Vehicle Production Engineering & Manufacturing Group. In April 2016, he was appointed as supervisor of plants across the in-house companies. In April 2017, he was made executive vice president, and also became chief officer of the Safety & Health Promotion Division.
https://newsroom.toyota.co.jp/en/corporate/companyinformation/officer/operating_officer/mitsuru_kawai.html
*****
monozukuri 或可翻譯成"日本"獨特"的製造東西"技術。
https://www.japantimes.co.jp/news/2018/04/15/business/corporate-business/hands-toyota-exec-passes-monozukuri-spirit/#.WtSGGYhubIU
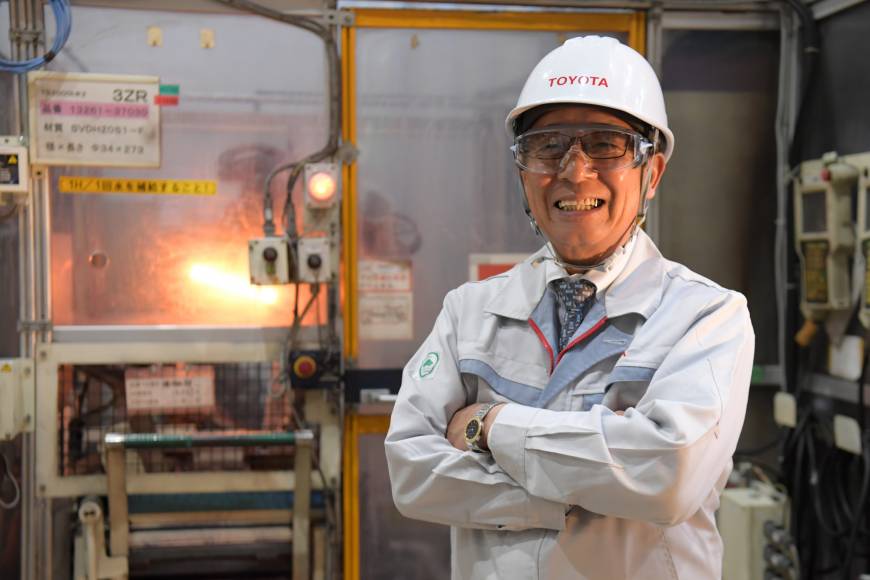
BUSINESS / CORPORATE | TAKING THE LEAD
Hands-on Toyota exec passes down monozukuri spirit
BY SHUSUKE MURAI
STAFF WRITER
TOYOTA, AICHI PREF. – Mitsuru Kawai drops by a bathhouse for factory workers at Toyota Motor’s headquarters in Aichi Prefecture each day before work.
After washing, the 70-year-old executive dons a helmet and heads for its noisy forging plant instead of his corporate office suite. There, he passes on his knowledge of craftsmanship to the younger factory workers, a daily routine that has remained the same since he was promoted to one of the automaker’s vice presidents in April 2017, the first graduate of Toyota Motor Corp.’s own vocational school to do so.
For Kawai, sitting in a cushy executive office chair holds no appeal.
“It’s suffocating to go somewhere where factory sounds and smells don’t exist,” Kawai said in an interview with The Japan Times. “The factory is where I grew up for over 50 years.”
“If I lose my touch, that will probably be the moment I find no reason to stay with this company.”
In an era where information technology and robotics are advancing enough to take over for people, Kawai continues to pour passion into passing on his know-how because he believes “only people with advanced skills can improve automation.”
“I know advanced artificial intelligence and IoT (the internet of things) are playing an increasingly important role in creating new products, including electric cars and automated driving systems. But after all, humans are the ones who created those things by using such technologies,” Kawai said. “You can’t let machines exploit you. You always need to be able to take advantage of machines by doing more than what the machines can do.”
Behind Kawai’s belief is a concern that the spirit of monozukuri— the philosophy in Japanese craftsmanship that puts emphasis on striving for better quality and continuous improvement — has weakened as more jobs have yielded to automation.
Monozukuri, which literally means “making things,” has long been Japan’s forte. But as robots have become ubiquitous in mass production, Kawai has noticed that more and more people are failing to doubt the quality of the work performed by machines and ceasing to use their own brains.
Kawai said experience tells him that people who lack an understanding of what machines are actually doing cannot contribute to improving the manufacturing process. He said he learned how to make cars on the factory floor before the automation age, when many aspects of production involved manual labor.
“I know how things are working behind automation. But today, a product can easily be made by just pressing a button.”
“What if machines produced defects? Young people today wouldn’t know what was wrong because everything is made inside the black box,” said Kawai, who graduated from Toyota Technical Skills Academy before joining the company in 1966.
“I am not saying automation is bad. We need more automation to increase efficiency and productivity,” he said. “But automation itself is not the goal.”
Kawai’s confidence in human craftsmanship comes from his more than five decades of experience forging engine parts from iron.
During his career, Kawai developed a keen intuition that robots cannot imitate. A skill allowed him to account for heat when welding iron plates so they would come out perfectly flat, or detect the source of a malfunction on a production line merely by sounds and smells.
Kawai said he still relies on his eyes to gauge the temperature of iron over 1,200 degrees by checking its color. If the digital thermometer reflects his estimate, he trusts the machine to perform the task.
“The point is, you need to be able to evaluate machines’ work by yourself,” he said. “Many young workers today are relying too much on machines, thinking that they are always right. And that’s what I’m worried about.”
Kawai’s concern is shared by Toyota President Akio Toyoda, who asked him to assume the executive position to pass on his expertise to the next generation.
At first, Kawai adamantly rejected the offer. But after 30 minutes jousting with Toyoda, he eventually compromised because the president asked him to take on the position “for the sake of the junior technicians.”
“I tend to oppose everything my boss tells me to do. But I do whatever I can do for my fellow junior colleagues,” he said with a laugh.
The history of Toyota is intertwined with the history of monozukuri.
The company’s origins can be traced back to 1918, when inventor Sakichi Toyoda established a company for automatic loom machines. In 1937, it branched out and started an automotive business.
Toyota’s pursuit of high-quality products is underpinned by the well-known concepts of kaizen (continuous improvement) and genba shugi (hands-on approach), plus the “just in time” inventory system, which was designed to reduce time and waste in production by shipping parts only when needed. These concepts have been adopted by other companies in Japan and abroad.
But Japan’s manufacturing prowess is at stake today as it struggles to catch up with the rapid spread of IT. The digital field, where many big companies in the U.S. and China have the upper hand, has become a major battleground for international competition.
Japan’s top reputation in manufacturing has been tarnished by scandals over the decades.
Last year, Kobe Steel Ltd. admitted to fabricating quality-control data on its products. Takata Corp.’s defective air bags have caused numerous deaths and massive recalls worldwide.
The vaunted automakers are also under a cloud of doubt.
Aside from the fuel-efficiency data manipulation scandal at Mitsubishi Motors Corp. in 2016, Nissan Motor Co. and Subaru Corp. admitted last year to letting unauthorized workers conduct final car inspections.
Although facing numerous challenges, Kawai said Japan’s manufacturers should maintain the tradition of monozukuri and keep developing creative frontline workers because “that’s where Japan’s competitiveness lies.”
If Japan fails on these fronts, he said, it will not be able to maintain an “efficient process in making high-quality products at the lowest possible cost.”
“That’s why I attach great importance to human workers who can take on difficult tasks and complete them thoroughly, no matter how challenging they are,” he said. “Because training such people is always needed for the Japanese manufacturing industry to win.”
Dad-like boss lauded as ‘bona fide craftsman’
For the younger workers, Mitsuru Kawai is more like their daddy than a corporate executive at a company with over 364,000 employees worldwide, said Masamitsu Shishido, project manager at the Forging Division of Toyota’s Honsha Plant.
“Of course, he is a great senpai (senior) to all of us, because he has become our vice president!” joked Shishido, who has worked with Kawai for about 40 years. “But he never tries to act bossy toward us. He always cares about the field where the real work is happening, trying to look after us.”
Shishido describes the 70-year-old as a “bona fide craftsman” who never compromises on the quality of his work.
“He is basically very kind,” Shishido said. “But in the field, he turns into a scary teacher. He allows no compromise at work.”
“Whenever we face trouble or need advice, he is always there to listen to us carefully. He takes it seriously and actually does things before he talks. That’s why we respect him,” he said.
The family-like bond among the employees is what has made the foundation of Toyota’s manufacturing strong, Kawai said.
When accepting an offer to become one of the top executives, Kawai was asked by Toyota President Akio Toyoda to be “a good role model for tens of thousands of factory workers to follow.”
“I have abundant experience, and I believe that’s the only merit I have,” Kawai said.
“My fellow junior workers have grown up by looking at how I work. They will listen to me and say: ‘I can’t deny what you say because that’s the way my daddy did it,’ ” he said.
*****
沒有留言:
張貼留言